A University at Buffalo–led research team is developing new catalysts that aim to turn climate-warming methane emissions into useful commercial products.
The work, described last month in Nature Communications, could impact numerous industries—including natural gas and crude oil production, livestock farming, landfilling and coal mining—where methane is a byproduct.
“There is an opportunity with methane to make more of an immediate impact in reducing climate-warming emissions. We’re working on a cost-effective solution to turn this industrial byproduct into valuable goods, such as chemical feedstocks,” says lead author Mark T. Swihart, SUNY Distinguished Professor and chair of the Department of Chemical and Biological Engineering in the UB School of Engineering and Applied Sciences.
Swihart, also a SUNY Empire Innovation Professor and faculty member in UB’s RENEW Institute, added that the technology has broader applications in semiconductors, biotechnology, electrochemistry and other fields in need of new and improved materials.
Shuo Liu, a Ph.D. candidate in Swihart’s lab, is first author of the study. Co-authors include Jeffery J. Urban, Ph.D., Chaochao Dun, Ph.D., Jinghua Guo, Ph.D., all members of the Lawrence Berkeley National Laboratory; Feipeng Yang, Ph.D., who was at Berkeley during the experiments but now works at Brookhaven National Laboratory; Qike Jiang of Westlake University in China; and Zhengxi Xuan, UB Ph.D. student.
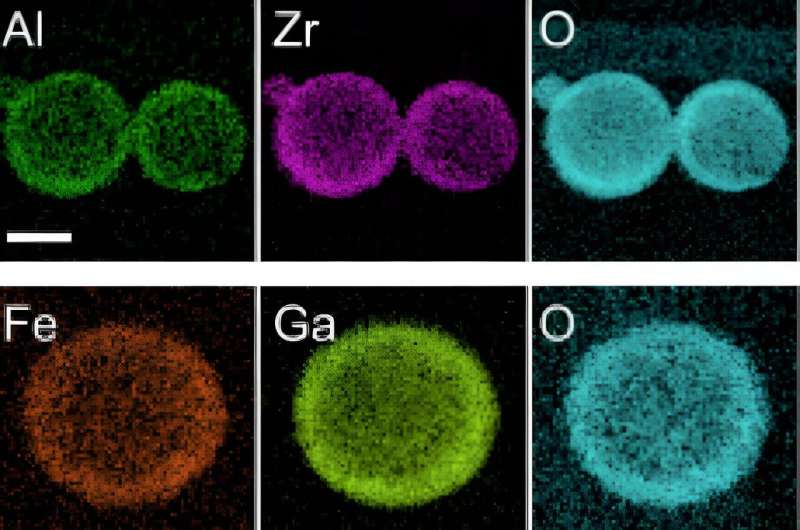
Methane capture lags behind carbon capture
Methane is the second most abundant greenhouse gas and the primary component of natural gas. It lasts only a few decades in Earth’s atmosphere compared to centuries for carbon dioxide, but methane traps 80 times more heat.
For decades, scientists have struggled to develop inexpensive ways to convert methane into useful products without producing carbon dioxide.
A possible solution is dry reforming, an industrial process that can convert both methane and carbon dioxide into chemical feedstocks, which are raw materials that manufacturers can use to create or process other products.
But dry reforming methane isn’t commercially viable because existing nickel-based catalysts stop working when their catalytically active particles become covered with carbon deposits (coking) or combine into larger, less active particles (sintering). Most catalysts also require complex production procedures.
Team uses unique flame reactor
To overcome these issues, the team utilized a unique flame reactor developed in Swihart’s lab that creates catalysts in one step. This aerosol-based process allowed the scientists to explore different, nickel-based catalysts, which in this case are tiny spherical particles called nanoshells.
“The key breakthrough is the flame aerosol synthesis method,” says Liu. “It allows us to overcome traditional limitations and create otherwise inaccessible materials with novel properties.”
The method produced its highest-performing catalysts by what the research team is calling an “encapsulated exosolution” process, in which nickel nanoparticles formed within the pores of an aluminum oxide shell rather than on its surface. This phenomenon helps build a more stable material that, in turn, creates a more durable catalyst.
In experiments, the team reported that, over the course of 640 hours at 800°C, the catalysts remained effective by converting 96% of methane and carbon dioxide into desired products. The results, the team says, dramatically outperform conventional catalysts.
The production method suggests a way forward not only to improved catalysts, but for other fields in which new materials are needed. This includes drug delivery, sensing and detection, energy storage and conversion, and coatings and surface modifiers, Swihart says.