An advancement in neutron shielding, a critical aspect of radiation protection, has been achieved. This breakthrough is poised to revolutionize the neutron shielding industry by offering a cost-effective solution applicable to a wide range of materials surfaces.
A research team, led by Professor Soon-Yong Kwon in the Graduate School of Semiconductors Materials and Devices Engineering and the Department of Materials Science and Engineering at UNIST has successfully developed a neutron shielding film capable of blocking neutrons present in radiation. This innovative shield is not only available in large areas but also lightweight and flexible.
The team’s paper is published in the journal Nature Communications.
“The developed MXene-Boron carbide composite shielding film is several tens of micrometers thick, over 1,000 times thinner than conventional commercial materials,” noted Professor Kwon. “It can be effortlessly applied to various surfaces, resembling the act of painting.”
Neutrons, which are integral to nuclear power generation, medical devices, and aerospace industries, possess inherent dangers when leaked. They can trigger unexpected phenomena in electronic devices or living organisms through interactions with other atoms.
The research team directly synthesized MXenes, a two-dimensional nanomaterial and the parent MAX phases. Additionally, they devised a technique to divide boron carbide into small pieces capable of absorbing neutrons and incorporated them between the maxillary layers. Based on this breakthrough, a large-area, flexible, and lightweight film was developed. Furthermore, a painting technique was devised to apply the developed mixture to diverse surfaces.
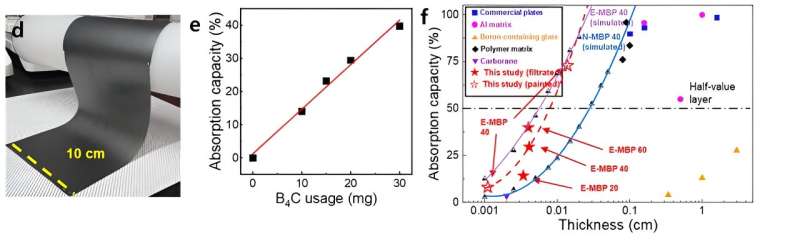
Co-first author Ju Hyoung Han, a researcher in the Department of Materials Science and Engineering at UNIST, stated, “By controlling the properties of MXene and boron carbide, we improved the stability of the mixture solution of the two materials. We successfully created a light and flexible shield with a stabilized MXene-boron mixture, which can be applied like paint on various objects’ surfaces, as demonstrated through experiments.”
The developed neutron shield possesses a dense structure with minimal bubble holes, measuring only several tens of nanometers. Consequently, it exhibits excellent mechanical properties compared to previously used polymer-based composites. Since additional processes such as heat treatment are unnecessary, a pure mixed structure without impurities can be manufactured.
Co-first author Si-Hyun, Seok, a researcher in the Department of Materials Science and Engineering at UNIST, commented, “Even after over 20,000 bending tests, the nylon composite coated with the shielding film maintained its circular shape up to 98%. It demonstrated an exceptional neutron shielding rate (40% when using 30mg) even with milligrams of boron carbide, showcasing its superiority.”
Professor Kwon added, “The newly developed composite manufacturing technology is practical and requires neither complex equipment nor processes. It enables the implementation of a neutron shielding coating film with the desired thickness and area. This study will expand the possibilities of MXene material coating technology and demonstrate its application in various fields.”