Oxidation can degrade the properties and functionality of metals. However, a research team co-led by scientists from City University of Hong Kong (CityU) recently discovered that severely oxidized metallic glass nanotubes can attain an ultrahigh recoverable elastic strain, outperforming most conventional super-elastic metals. They also discovered the physical mechanisms underpinning this super-elasticity.
Their discovery implies that oxidation in low-dimension metallic glass can result in unique properties for applications in sensors, medical devices and other nanodevices. The findings were published in Nature Materials under the title “Oxidation-induced superelasticity in metallic glass nanotubes.”
In recent years, the functional and mechanical properties of low-dimensional metals, including nanoparticles, nanotubes and nanosheets, have garnered attention for their potential applications in small-scale devices, such as sensors, nano-robots and metamaterials. However, most metals are electrochemically active and susceptible to oxidation in ambient environments, which often degrades their properties and functionalities.
“Metallic nanomaterials have a high surface-to-volume ratio, which can be up to 108 m-1. So in principle, they are expected to be particularly prone to oxidation,” said Professor Yang Yong, in the Department of Mechanical Engineering at CityU, who led the research team together with his collaborators.
“To use low-dimensional metals to develop next-generation devices and metamaterial, we must thoroughly understand the adverse effects of oxidation on the properties of these nanometals and then find a way to overcome them.”
Therefore, Professor Yang and his team investigated oxidation in nanometals, and in sharp contrast to their expectation, they found that severely oxidized metallic glass nanotubes and nanosheets can attain an ultrahigh recoverable elastic strain of up to about 14% at room temperature, which outperforms bulk metallic glasses, metallic glass nanowires, and many other super-elastic metals.
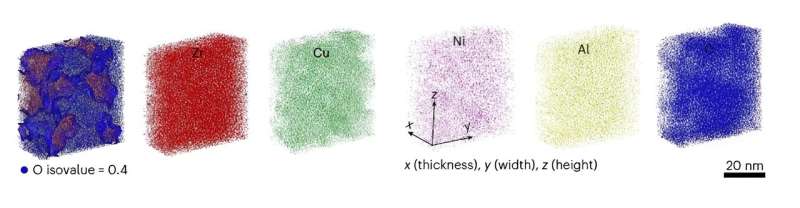
They made metallic glass nanotubes with an average wall thickness of just 20 nm, and fabricated nanosheets from different substrates, such as sodium chloride, polyvinyl alcohol and conventional photoresist substrates, with different levels of oxygen concentration.
They then conducted 3D atom probe tomography (APT) and electron energy loss spectroscopy measurements. In the results, oxides were dispersed within the metallic glass nanotubes and nanosheets, unlike conventional bulk metals, in which a solid oxide layer forms on the surface. As the oxygen concentration in the samples increased owing to metal–substrate reactions, connected and percolating oxide networks were formed inside the nanotubes and nanosheets.
In-situ microcompression measurements also revealed that the severely oxidized metallic glass nanotubes and nanosheets exhibited a recoverable strain of 10%–20%, which was several times more than that of most conventional superelastic metals, such as shape memory alloys and gum metals. The nanotubes also had an ultra-low elastic modulus of about 20–30 GPa.
To understand the mechanism behind this, the team conducted atomistic simulations, which indicated that the superelasticity originates from severe oxidation in the nanotubes and can be attributed to the formation of a damage-tolerant percolation network of nano-oxides in the amorphous structure. These oxide networks not only restrict atomic-scale plastic events during loading, but also lead to the recovery of elastic rigidity on unloading in metallic glass nanotubes.
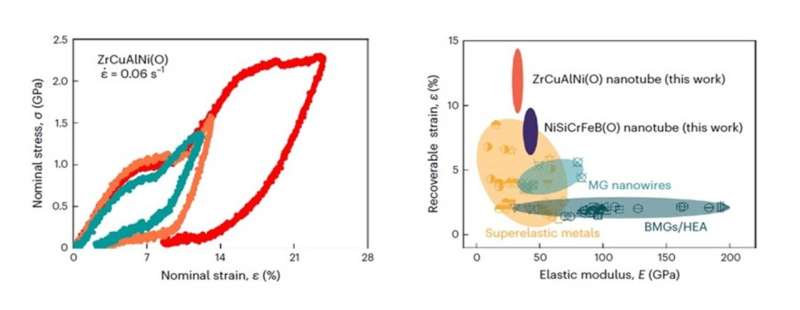
“Our research introduces a nano-oxide engineering approach for low-dimensional metallic glasses. The morphology of nano-oxides within metallic-glass nanotubes and nanosheets can be manipulated by adjusting the oxide concentration, ranging from isolated dispersions to a connected network,” said Professor Yang.
“With this approach, we can develop a class of heterogeneous nanostructured ceramic-metal composites by blending metals with oxides at the nanoscale. Such composites have great potential for various future commercial applications and nanodevices working in harsh environments, such as sensors, medical devices, micro- and nano-robots, springs and actuators,” he added.